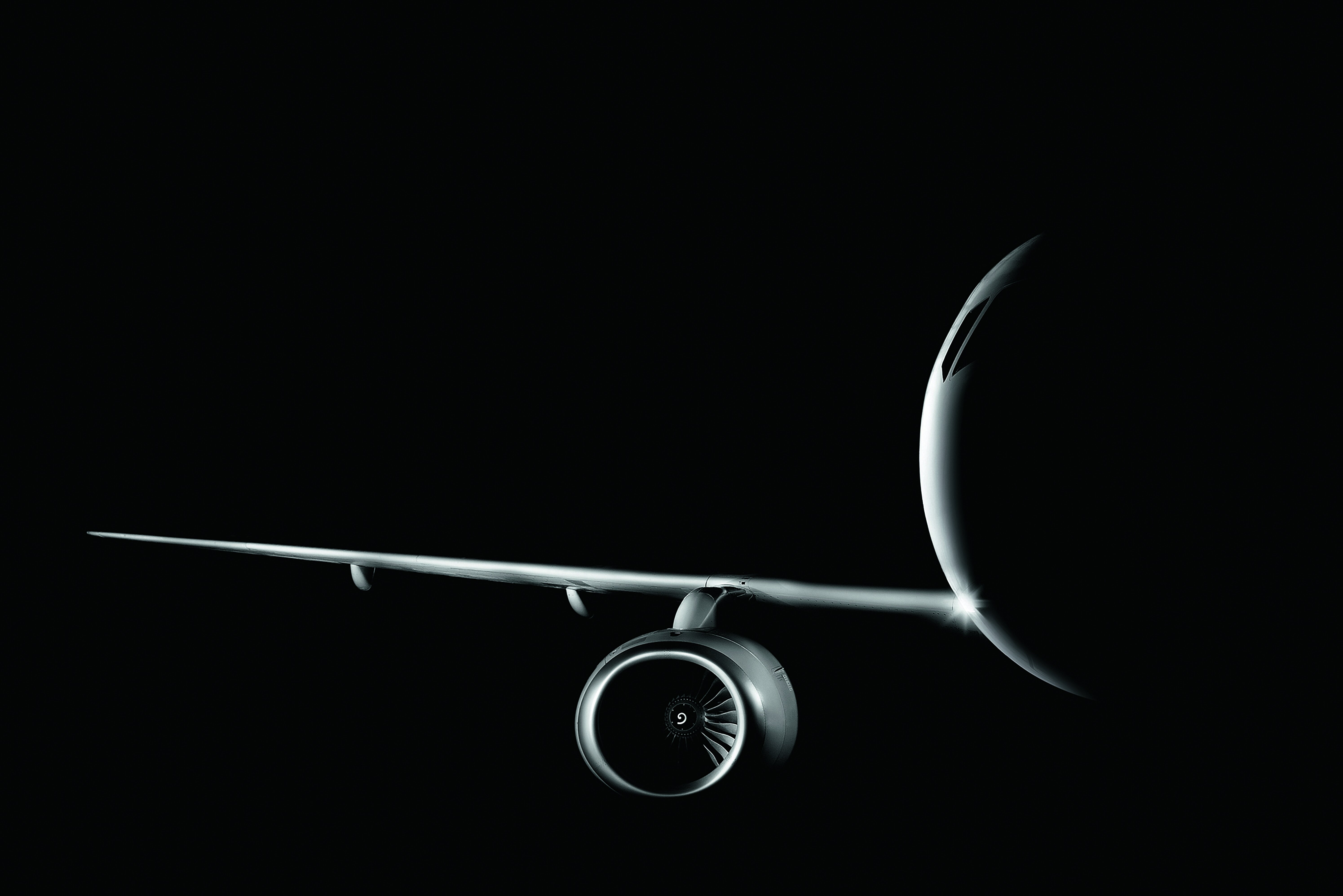
Michael Oluwatosin Bodunrin
Wits University
South African researchers are poised to fundamentally change the titanium industry, through developing a way to make less expensive titanium.
Titanium is abundant in South Africa and is as strong as steel, but much lighter – which makes it an important metal for the aerospace industry, where it is used extensively in air- and spacecraft. South Africa is among the top producers of titanium ore in the world and there are efforts to set up a robust titanium industry in the country, rather than simply exporting the ore. Beneficiating our titanium would mean that both commercial and the less expensive experimental titanium products could be made from local raw materials and become a large source of foreign revenue.
But the metal is difficult to process. For this reason, although titanium was first discovered in 1791, it took more than a century to put it to use. It has a strong affinity for air, which means unless handled carefully the metal binds with air at high temperatures and becomes brittle and weaker.
Because of these difficulties, titanium is prohibitively expensive, and its applications are limited.
For example, although it has comparable strength to steel and is less likely to rust, you are unlikely to find titanium in car parts or as structural elements in buildings. They are made from steel because steel is stable, easy to process, and, importantly, affordable.
But steel in cars adds to their weight, and thus their fuel consumption and environmental pollution. Its use in manufacturing and construction is also problematic because steel corrodes easily in most industrial environments. This can lead to plants breaking down and large economic losses.
The answer to these problems could lie in titanium, but only if we can make it cheaper.
This is one of our research focuses at the Centre of Excellence in Strong Materials, based at the University of Witwatersrand.
By mixing titanium with other metals, we can make it stronger. These mixtures are called alloys.
The process of making an alloy is similar to making bread: you add certain amounts of specific ingredients to flour to create the kind of bread you want. Many alloys, including titanium alloys, are produced by mixing two or more types of metals in the right proportion. These ratios give the alloys certain properties and thus a wide range of applications.
The most used titanium alloy, known as Ti-6Al-4V, contains titanium, but with 6% aluminium and 4% vanadium, a shiny silver metal, mixed in. If you have a cup of the Ti-6Al-4V alloy, it would contain about a tablespoon of aluminium and a teaspoon of vanadium.
This alloy accounts for more than half of the global titanium market. It is preferable to pure titanium because the presence of aluminium and vanadium stabilises the alpha and beta phases respectively. Phases are the ways in which the atoms can arrange themselves inside the alloy, like serviettes folded into different shapes. They are the building blocks that make up Ti-6Al-4V and can only be seen with the help of a microscope.
These phases are like the red and white blood cells in your blood: Both cells are necessary but they only work well when they are in the correct proportion. Pure titanium would consist of only the alpha phase – in which the atoms collect into hexagons – at room temperature, but these would transform into beta phase – configured into cubes – at higher temperatures. The role of vanadium is to ensure that the titanium retains the beta phase (cubes) at room temperature. By tweaking these phases in the alloys, materials engineers select the material’s properties.
Titanium itself is expensive, but adding costly alloying elements like vanadium make the alloy even more expensive. The cost of titanium alloys can be reduced by either using cheaper alloying metals or improving the way that we make products out of titanium, so that less titanium is wasted. (Wastage is a major factor in the high price of titanium.)
At the University of Witwatersrand, researchers in the Centre of Excellence in Strong Materials are trying to substitute expensive vanadium with iron, which is very cheap and capable of stabilising the beta phase. We have found that iron can also make the titanium alloy even stronger. Although this approach is not new to researchers working in this field, the problem they often encounter is that, when they add about 3% iron or more to titanium, it does not stabilise the beta phase but forms clumps of metal. It is similar to adding too much Cremora powder to a cup of coffee: you get congealed clumps rather than a well-blended hot beverage.
To prevent the formation of these clumps, known as intermetallic compounds, we are developing an experimental alloy. We are not replacing all the vanadium with iron but only partially substituting it. Retaining some vanadium in our alloys may prevent iron from forming clumps with titanium.
We have played with the amount we substituted, varying it between 1% and 3%. Our goal was to see how much the material’s behaviour changed as we added more iron to the alloy. Increasing the iron content to 3% and reducing the vanadium content to 1% helped to increase the amount of cube-shaped beta phase in the alloy and the hardness also increased.
A major concern, though, is that iron reacts badly to salty water. But as long as we kept the iron levels below 4%, it didn’t make the alloy more likely to rust. In addition, a little dose of 1% vanadium was sufficient to suppress the formation of the clumps which could have made the alloy very brittle.
From the results obtained so far, it appears that our alloys, with their unique combination of iron and vanadium, might be a cheaper alternative to Ti-6Al-4V. Our alloys can be produced locally, and could grow the possible applications for titanium. But we still need to do more research before it is scaled-up. The ultimate goal is to identify the best processing conditions for shaping and forming this alloy into finished goods, such as wheel hubs, bicycle frames, and jewellery. This would help industries to avoid expensive trial and error when processing the alloy into finished products – and could bring lighter, stronger cars or kitchen utensils onto the market.
Leave a Reply